鈑金加工剪切辦法是一對(duì)翻滾方向相反的圓盤剪刃對(duì)板料進(jìn)行剪切,機(jī)箱機(jī)柜剪切是指將原材料按照需要將其剪切成所需形狀的材料,同時(shí)也可以經(jīng)過(guò)剪板機(jī)得到矩形工件的工藝過(guò)程。剪切材料厚度為機(jī)床額定值的各種鋼板、銅板、鋁板及非金屬材料板材,而且必須是無(wú)硬痕、焊渣、夾渣、焊縫的材料,不允許超厚度,嚴(yán)禁超負(fù)荷使用剪板機(jī)。不得剪切淬火鋼料和硬質(zhì)鋼、高速鋼、合金鋼、鑄件及非金屬材料。
The cutting method for sheet metal processing involves a pair of disc cutting edges with opposite rolling directions to cut the sheet metal. The cutting of the chassis and cabinet refers to the process of cutting raw materials into the desired shape according to needs, and also the process of obtaining rectangular workpieces through a plate shearing machine. Various steel plates, copper plates, aluminum plates, and non-metallic materials with a thickness equal to the rated value of the machine tool must be cut, and must be free of hard marks, welding slag, slag inclusions, and weld seams. Excessive thickness is not allowed, and overloaded use of the cutting machine is strictly prohibited. Do not shear quenched steel materials, hard steel, high-speed steel, alloy steel, castings, and non-metallic materials.
下面是鈑金件、剪切要求僅供參考:
The following are sheet metal parts and cutting requirements for reference only:
一、機(jī)箱機(jī)柜鈑金件、剪切要求
1、 Requirements for sheet metal parts and cutting of chassis and cabinet
剪切斷面:鈑金件因剪切粗糙,對(duì)于氧化、電鍍或噴塑件,剪切端面要工藝應(yīng)增加打磨拋光工序;
Cutting section: Due to rough cutting of sheet metal parts, for oxidation, electroplating, or spray molded parts, the cutting end face should be processed by adding polishing processes;
剪切平行度:剪切平行度約為0.3%,當(dāng)零件精度高于該值時(shí),工藝應(yīng)采取其它方式下料;
Shear parallelism: The shear parallelism is about 0.3%. When the accuracy of the part exceeds this value, the process should adopt other methods of cutting;
剪切毛刺:剪板機(jī)剪切毛刺約為板厚4~6%,當(dāng)毛刺大于0.1時(shí),需要增加去毛刺工序。
Cutting burrs: The shearing machine cuts burrs about 4-6% of the plate thickness. When the burrs are greater than 0.1, an additional deburring process is required.
二、剪切間隙選擇
2、 Cutting gap selection
剪切間隙:按材質(zhì)、板厚選擇剪切間隙能保證零件剪切質(zhì)量和設(shè)備剪切,所以正確選擇剪切間隙尤為重要。
Shearing gap: Choosing the cutting gap based on material and plate thickness can ensure the quality of part cutting and the safety of equipment cutting, so it is particularly important to choose the correct cutting gap.
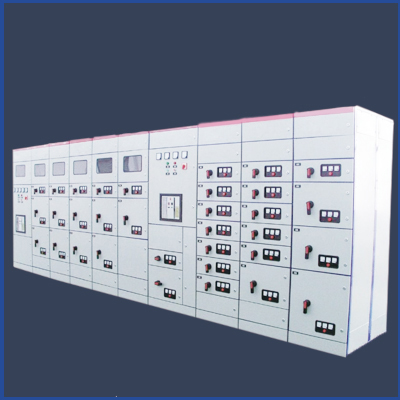
三、剪切角度選擇
3、 Cutting angle selection
剪切角度選擇:按材質(zhì)、板厚選擇剪切角能提高零件的剪切質(zhì)量;對(duì)于相同材質(zhì)及板厚的零件,若剪切角取小值,零件剪切的扭曲變形的相對(duì)減小、剪切質(zhì)量提高;相反,零件的扭曲變形相對(duì)增大,剪切質(zhì)量則降低。
Cutting angle selection: Selecting a cutting angle based on material and plate thickness can improve the cutting quality of the part; For parts of the same material and plate thickness, if the shear angle is taken as a small value, the relative reduction of deformation caused by the part's shear and the improvement of shear quality will be achieved; On the contrary, the twisting deformation of the parts increases relatively, while the shear quality decreases.
四、剪切間隙及調(diào)整
4、 Shear clearance and adjustment
影響零件剪切質(zhì)量的主要因素是剪切間隙,所以操作工必須依據(jù)剪切的材質(zhì)及厚度,通過(guò)旋轉(zhuǎn)機(jī)床上的刻度盤,將上、下切刀間隙調(diào)整到板材剪切的規(guī)定范圍。
The main factor affecting the cutting quality of parts is the cutting gap, so operators must adjust the gap between the upper and lower cutting knives to the specified range for sheet cutting by rotating the dial on the machine tool based on the material and thickness of the cutting.
五、上下切刀及后檔
5、 Upper and lower cutting knives and rear gear
鈑金件剪切通過(guò)機(jī)床系統(tǒng)中程序控制各機(jī)構(gòu)相互動(dòng)作,由上、下刀片完成剪切;剪切平行度則是由后擋及下切刀之間的平行精度保證。
The cutting of sheet metal parts is controlled by the program in the machine tool system to control the mutual action of various mechanisms, and the cutting is completed by the upper and lower blades; The parallelism of shearing is ensured by the parallelism accuracy between the rear gear and the lower cutting tool.
在生產(chǎn)實(shí)力上,潤(rùn)博機(jī)電已經(jīng)步入工業(yè)4.0,從超國(guó)標(biāo)要求的原材料入庫(kù)質(zhì)檢,到自動(dòng)化的生產(chǎn)線設(shè)備、再到機(jī)加環(huán)節(jié)度達(dá)0.1mm的高標(biāo)準(zhǔn),每一個(gè)環(huán)節(jié)、每一道工序都保證了鈑金加工工藝的標(biāo)準(zhǔn)化,確保機(jī)箱機(jī)柜產(chǎn)品的高質(zhì)產(chǎn)出。
In terms of production strength, Runbo Electromechanical has entered Industry 4.0, from raw material warehousing and quality inspection that exceeds the national standard requirements, to automated production line equipment, and to the high standard of 0.1mm in machining processes. Every step and process ensures the standardization of sheet metal processing technology, ensuring the high-quality and efficient output of chassis and cabinet products.